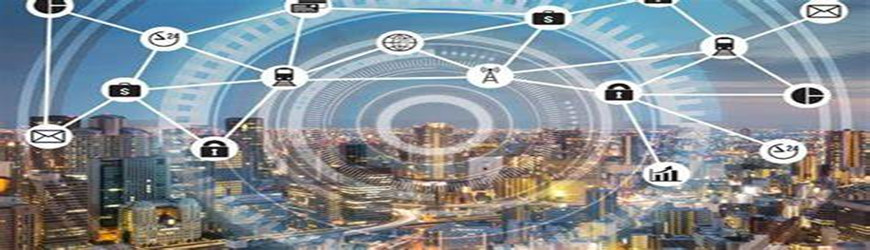
On September 3, 2021 China Smart Industry Forum was held in Beijing Shougang Park. This forum was one of the forum activities of the Service Trade Fair, with the theme of "Smart Era Leading the Future". Hou Shengli, vice president of Cisco Greater China, attended and delivered a speech.
Hou Shengli said in his speech that with the further deepening of digital transformation and the continuous emergence of smart manufacturing or Industry 4.0, it can be seen that IT and OT continue to merge. On the basis of this connection, IT will have a deeper integration with AI and OT, and will provide a variety of data. After it is provided, there will be additional work, such as how to do intelligent analysis, see Production efficiency, the state of the equipment itself, how to improve the utilization rate of the equipment.
Another very important point is how to reduce its risk, or reduce its usual situation, to make predictions and see when the equipment will be down based on the AI data, or need to undergo various levels of overhaul, so as to ensure production performance. Continuous completion. In addition, because previously isolated systems or different systems were opened up, many new business models and many new business methods would be created.
Hou Shengli pointed out that if you do a smart factory, from the perspective of a standard industrial model, it has a few layers of architecture. You can see that L0, L1, and L2 are more of the production lines of the factory controlled by the original system. These smart devices are on. The third layer is the network layer. Between the network layer and the real application, the 3.5 layer is the industrial EMZ zone, that is, the industrial production network will have higher reliability, and it must have very good redundancy. There must be no virus damage. There will be an isolation here. Go up to the traditional ERP or these OA applications within the enterprise itself. In this, we will see that among the different levels, first of all, the tradition is that there is such a distinction in the 3.5 layer, going down to OT, and going up to IT. With the transformation of informatization or intelligentization, after intelligent manufacturing, we will see IT will enter the network layer or connection layer from the 3.5 layer down, where these devices will be more intelligent, will support the Ethernet protocol, will have their own address, connect to us, can analyze, manage, and control.
Hou Shengli talked that if the first step in smart manufacturing is basic connectivity, the following major problems will be seen after connectivity:
First, how to ensure that the production line is safe and reliable due to network problems and physical problems. It often happened in the past. For example, a semiconductor company's production line was threatened by ransomware, the production line was controlled by others, and the data was encrypted by others, and normal production could not be carried out. In addition, how can employees help the entire production line have more automated control? The equipment of these production lines should be very intelligent, and how can employees have a good way to manage and use this system well.
Second, the empowerment of employees is a way of remotely guiding on-site workers to perform corresponding operations through remote expert tutoring and video or voice support. In addition, it is the end-to-end control on the production line, as well as its own control mechanisms such as security firewalls or secure access on industrial equipment to ensure that only customers with certain permissions can log in to the system.
Third, how to ensure overall safety control and prevent the production line from being hijacked by others.
Fourth, many factories or smart manufacturing today need to realize flexible manufacturing.
Fifth, edge computing. When doing these industrial productions, you may hear that, for example, edge computing, formerly called distributed computing or cloud computing, cloud computing requires a time delay for a long time, in the production line of industrial production. , There is no way to transfer the data to the cloud and analyze it again. There must be a small edge computing center locally to do real-time data processing or real-time data analysis and take corresponding actions. At the same time, these data can be transmitted to the remote cloud center for comparison, analysis, and storage. It can be seen that when doing Industry 4.0 or a lighthouse factory or a smart factory, there will be various technologies behind to meet your needs.